多霍尔元件提高飞轮转速测量精度应用
飞轮通常采用无铁芯结构的三相无刷直流电动机作为驱动部件,采用码盘或霍尔元件作为无刷直流电动机的位置传感器。位置传感器的作用有两个:一是检测转子在运动过程中的位置;二是形成飞轮的测速脉冲,以便于上位机采集并计算飞轮转速。飞轮旋转一周得到的测速脉冲数量直接决定飞轮的调速性能,进而影响飞轮的转速控制精度。
目前,飞轮所采用的传统的三霍尔测量器件存在测速精度低的缺点,其原因在于电动机旋转一周仅能产生3倍于极对数的测速脉冲数,因此在需要频繁过零调速。并强调低速平稳性的飞轮中应用较少。采用码盘作为飞轮的位置传感器可以得到更多的脉冲数,但采用码盘存在结构复杂、体积大、成本高、可靠性差的问题。
飞轮转速测量精度分析
某工程任务对飞轮具体要求如下:飞轮采用的三相8对极磁钢结构的无刷直流电动机。电动机外转子直径100mm,与上位机通讯指令周期为2s,飞轮转速的控制精度优于约6°/ s, 即1r/min。上位 机测速采用测频法,转速脉冲上、下沿计数。考虑上位机通讯指令周期为2s,取飞轮转速采样周期为1.5s,测量最小误差为±1个(2个)转速脉冲,(即1.5s里要有2个)则要求在9°机械角范围内至少均匀分布2个位置脉冲,即每转80个转动脉冲。
以往的三霍尔测量器件构成的飞轮转速反馈仅能提供最多每转24个转速脉冲(霍尔数x磁钢极对数),其转速精度为4r/min,显然无法满足使用要求。在电动机结构不改变的情况下,需要将霍尔数量增加到12个(3的整数倍)。以提供最多每转96个转动脉冲、192个计数边沿用于测速。以满足飞轮每转80个以上的转速脉冲的要求。
多霍尔元件安装布局的具体设计
图1所示为环氧浇铸前的电动机定子骨架,通常的做法是在骨架的突起处开槽(图1霍尔安装处),用于安装霍尔。安装完成后再进行环氧浇铸,将霍尔固封在定子骨架内部。这种做法的缺点在于:
①不易维修。尤其是定子进行环氧浇铸后,如果发生霍尔元件失效情况,只能更换整个电动机定子。
②器件定位精度差。对于多霍尔安装时,无法对转速信号相位进行调整以达到较高位置精度的要求。
针对原有的霍尔安装方式带来的缺点,改变器件的安装位置如图2所示,将器件安装在电动机定子的外衬套圆周边沿上。利用转子磁钢边沿的磁场激发器件的状态改变。这种做法可以有效地克服原有的霍尔安装方式的缺点。需要注意的是设计时在磁钢端面和霍尔元件之间需要留有合适的间隙,既要保证有足够的磁场强度以激发霍尔,又要保证两者。不会因间隙过小发生机械干涉,导致飞轮卡死。
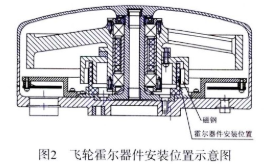
下面结合图2、图3进行多霍尔具体设计的说明,按照数量增加到12个的具体要求,在一对极的磁钢构成一个电周期的情况下在一个电周期内12个霍尔信号将产生12个转速脉冲(也即24个信号边沿,上升和下降沿)用于测速。飞轮电动机为 8对极,则每对极磁钢的机械角度为45°。这就意味着要在这样一个机械角度内沿电动机定子边沿镶嵌12个霍尔,每个霍尔相隔的机械角度为3。75°,而一对极磁钢对应的电动机定子边沿弧长仅为39mm,霍尔元件自身宽度4mm,显然在一-对极磁钢的机械角度内安装12个霍尔是无法实现的,针对这种情况在本设计中对霍尔的分布进行分组处理,将12个霍尔平均分成4组,按每组内3个霍尔相差机械角度15° 。如图3所示。即一个电周期内三个霍尔电角度相差120° , 每组霍尔元件与相邻的一组相差机械角度3。75° , 在电动机定子圆周上进行分布,采用这种分组方式主要出于两方面考虑:
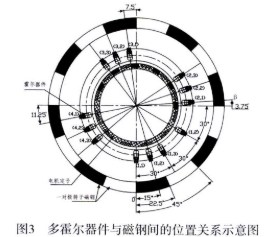
①对于三相六状态的无刷直流电动机而言,这样的分组方式使每组霍尔均可用于电动机换相(需在软件中进行一定的相位补偿),当一组霍尔用于电动机换相的主份时,其余各组可看作该主份的备份,有利于提高设计的冗余度与可维修性。
②可将每组霍尔预埋在单独设计的滑块上,利用滑块在安装圆周上的滑动来调节组与组之间的相对位置,进而达到调整脉冲信号边沿相位的目的。
电动机旋转时霍尔输出信号时序如图4所示,从图4中可以看出,在每对极磁钢对应的电周期内都会有24个由霍尔元件产生的边沿信号用于测速,电动机旋转一周将产生192个边沿信号。
目前,飞轮所采用的传统的三霍尔测量器件存在测速精度低的缺点,其原因在于电动机旋转一周仅能产生3倍于极对数的测速脉冲数,因此在需要频繁过零调速。并强调低速平稳性的飞轮中应用较少。采用码盘作为飞轮的位置传感器可以得到更多的脉冲数,但采用码盘存在结构复杂、体积大、成本高、可靠性差的问题。
飞轮转速测量精度分析
某工程任务对飞轮具体要求如下:飞轮采用的三相8对极磁钢结构的无刷直流电动机。电动机外转子直径100mm,与上位机通讯指令周期为2s,飞轮转速的控制精度优于约6°/ s, 即1r/min。上位 机测速采用测频法,转速脉冲上、下沿计数。考虑上位机通讯指令周期为2s,取飞轮转速采样周期为1.5s,测量最小误差为±1个(2个)转速脉冲,(即1.5s里要有2个)则要求在9°机械角范围内至少均匀分布2个位置脉冲,即每转80个转动脉冲。
以往的三霍尔测量器件构成的飞轮转速反馈仅能提供最多每转24个转速脉冲(霍尔数x磁钢极对数),其转速精度为4r/min,显然无法满足使用要求。在电动机结构不改变的情况下,需要将霍尔数量增加到12个(3的整数倍)。以提供最多每转96个转动脉冲、192个计数边沿用于测速。以满足飞轮每转80个以上的转速脉冲的要求。
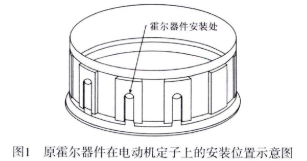
多霍尔元件安装布局的具体设计
图1所示为环氧浇铸前的电动机定子骨架,通常的做法是在骨架的突起处开槽(图1霍尔安装处),用于安装霍尔。安装完成后再进行环氧浇铸,将霍尔固封在定子骨架内部。这种做法的缺点在于:
①不易维修。尤其是定子进行环氧浇铸后,如果发生霍尔元件失效情况,只能更换整个电动机定子。
②器件定位精度差。对于多霍尔安装时,无法对转速信号相位进行调整以达到较高位置精度的要求。
针对原有的霍尔安装方式带来的缺点,改变器件的安装位置如图2所示,将器件安装在电动机定子的外衬套圆周边沿上。利用转子磁钢边沿的磁场激发器件的状态改变。这种做法可以有效地克服原有的霍尔安装方式的缺点。需要注意的是设计时在磁钢端面和霍尔元件之间需要留有合适的间隙,既要保证有足够的磁场强度以激发霍尔,又要保证两者。不会因间隙过小发生机械干涉,导致飞轮卡死。
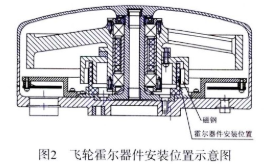
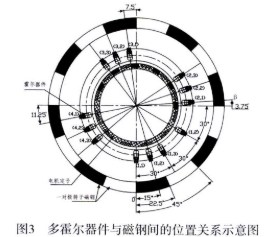
②可将每组霍尔预埋在单独设计的滑块上,利用滑块在安装圆周上的滑动来调节组与组之间的相对位置,进而达到调整脉冲信号边沿相位的目的。
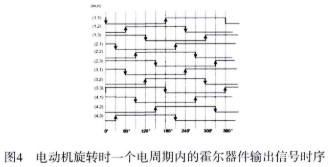
电动机旋转时霍尔输出信号时序如图4所示,从图4中可以看出,在每对极磁钢对应的电周期内都会有24个由霍尔元件产生的边沿信号用于测速,电动机旋转一周将产生192个边沿信号。
下一篇:霍尔元件在自动变速箱控制器中的应用 上一篇:霍尔开关在无刷直流电机控制中的应用